Dans les conditions de développement dynamique des processus de l'économie moderne, la création de procédures de production et de contrôle de plus en plus complexes, l'une des approches les plus pertinentes pour leur amélioration est l'introduction de méthodes d'optimisation des pertes diverses. Tout d'abord, cela concerne les ressources des entreprises - temporaires, financières, technologiques, énergétiques et autres.
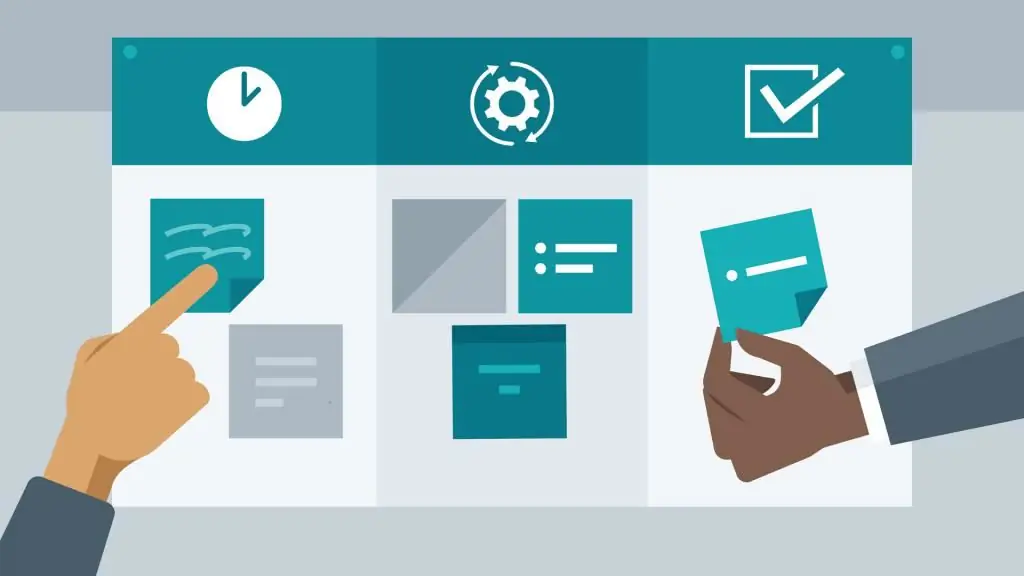
Caractéristiques de l'activité
En pratique, il existe un certain plafond, qui est associé au niveau de développement technologique et organisationnel du système (organisation, entreprise). Il est clair qu'il est inopportun d'exiger une automatisation totale de la production d'un petit atelier de couture selon divers critères, et surtout économiques. Cependant, quelle que soit la taille du système, il est nécessaire d'assurer l'utilisation maximale et optimale des ressources disponibles avec un minimum de pertes, ce qui est vrai pour toute organisation et activité.
Dans ce cas, il devient nécessaire d'utiliser des techniques de gestion de processus progressives basées sur la théorie de la création d'une production allégée ou "lean". Il s'agit notamment des systèmes 5S et TPM, de la cartographie des flux de valeur et du SMED, etc.
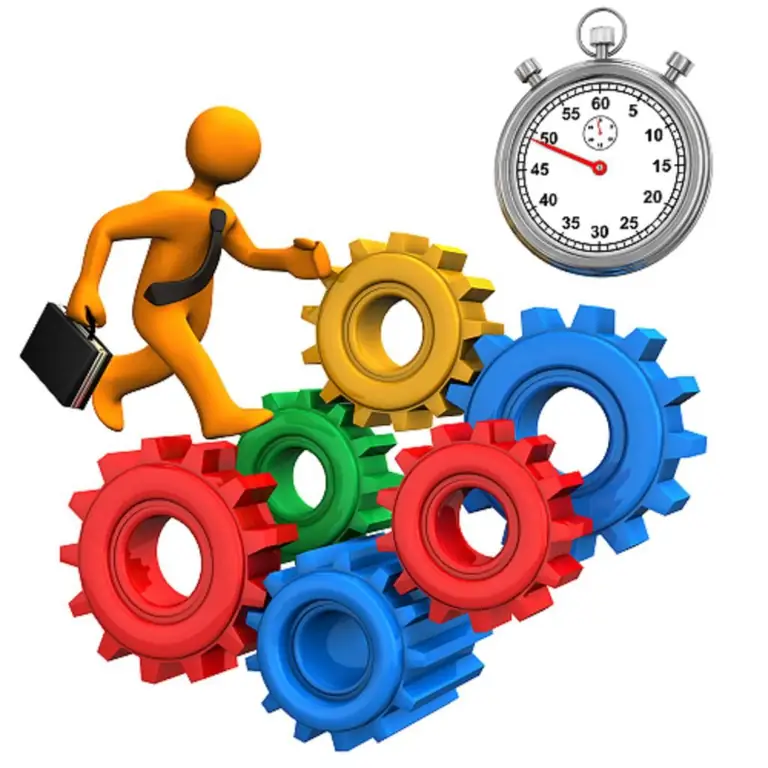
Le but de l'innovation
La production allégée («lean») est un système d'approches spéciales de l'organisation des activités, qui considère comme objectif principal l'élimination de diverses pertes dans le système. Le mécanisme est assez simple: tout ce qui n'apporte pas de valeur ajoutée au client doit être classé comme redondant (déchet) et retiré du système. Il est clair que la notion de "pertes" est la pierre angulaire, puisque leur définition affectera directement l'efficacité de la méthode. Dans ce cas, apprendre à cartographier le flux de valeur de vos spécialistes est un avantage significatif sur le marché de la prestation de services
Types de pertes
Le "Lean Manufacturing" est l'un des concepts fondamentaux de la logistique de production. Et bien qu'il existe plusieurs approches différentes pour déterminer les pertes, nous distinguerons les types les plus universels:
- Temps d'attente - tout temps d'arrêt dans les activités réduit la valeur du produit final. L'attente de matériaux, de réparations d'équipements, d'informations ou de directives de la part de la direction ralentit le processus et augmente le coût de sa mise en œuvre.
- Opérations inutiles (traitement inutile des produits) - opérations technologiques inutiles, étapes de projet, tout ce quifournis par les procédures standard, mais peuvent être nivelés sans perte de confiance du client.
- Déplacements inutiles de travailleurs - recherche d'outils, d'équipements, mouvements irrationnels dus à une mauvaise organisation du lieu de travail, etc.
- Mouvement inutile de matériaux - mauvaise organisation du système d'inventaire, manque de logistique de transport progressive et de mécanismes d'externalisation de la logistique.
- Inventaire excédentaire: immobilise le fonds de roulement d'une organisation en raison de dépenses élevées en articles de stock excédentaires.
- Déchets technologiques - systèmes de traitement de données, processus technologiques et voies de traitement obsolètes.
- Pertes de surproduction - la production d'une quantité excessive de produits, ce qui entraîne une augmentation du coût de son stockage, de son transport et de sa vente ultérieure.
- Pertes intellectuelles - manque de mécanismes pour encourager l'initiative des travailleurs et des employés, faiblesse du système de propositions de rationalisation, suppression d'une approche créative du travail.
L'une des méthodes les plus courantes pour éliminer le gaspillage du système et rationaliser l'exécution des projets est la cartographie des flux de valeur. La fabrication au plus juste vous permet en même temps de créer un système adaptatif qui répond avec souplesse aux changements de l'environnement.
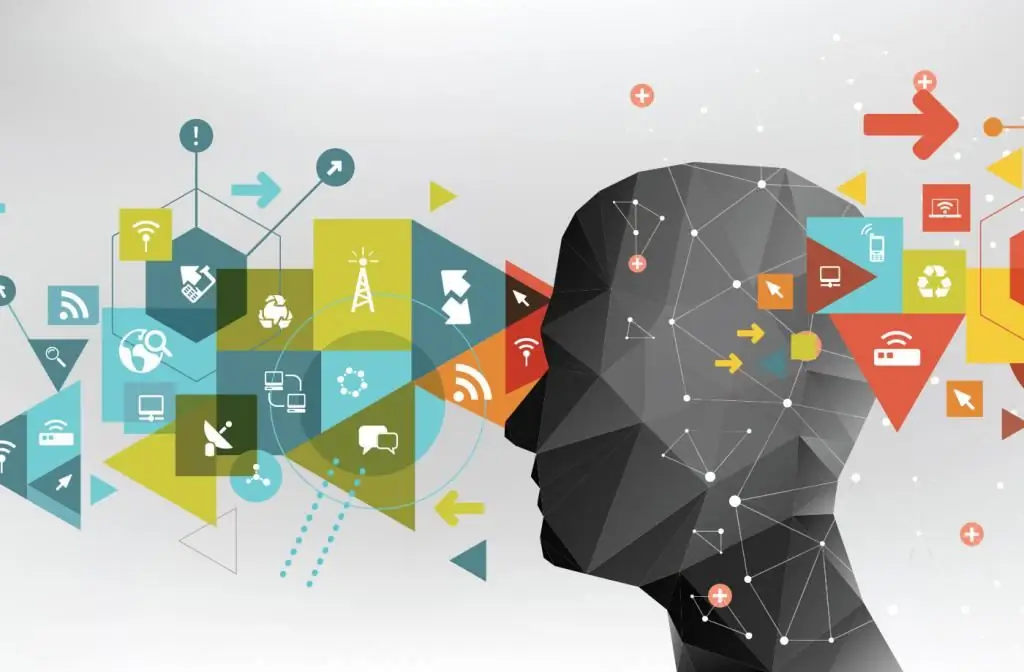
Flux de valeur
Le flux de valeur est un ensemble de toutes les actions (opérations) qui sont effectuées sur un produit afin d'atteindrel'état requis ou l'obtention des caractéristiques requises. Les actions sont différenciées en deux groupes:
- création de la valeur du produit (ajout de valeur);
- n'ajoute pas de valeur au produit.
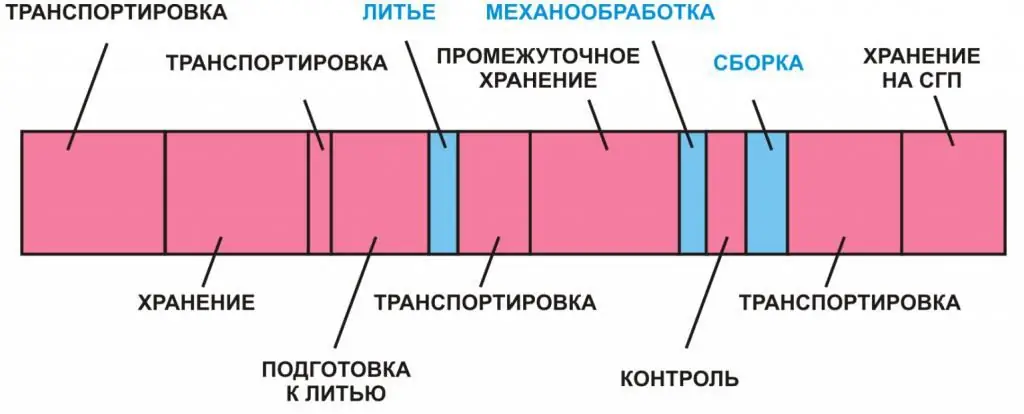
Comme on peut le voir sur la figure présentée, les étapes du changement technologique du produit (couleur bleue) ajoutent de la valeur au produit, et les étapes des opérations auxiliaires - préparation, transport, stockage - (couleur rose) - au contraire, réduisez plutôt la valeur du produit en raison de pertes de temps inutiles.
Processus de mappage
La base de la technique de cartographie est le développement d'un algorithme graphique spécial qui montre le processus de création de produits (mise en œuvre du projet) dans le temps. Cet algorithme est appelé une carte de flux de valeur, qui est un modèle graphique basé sur un ensemble spécifique de symboles (signes, symboles).
Les principaux avantages de la carte:
- obtenir un modèle graphique du processus en cours, en tenant compte de divers processus supplémentaires pour une perception visuelle holistique (la tâche est de voir le flux général des événements);
- la capacité à détecter différents types de pertes à toutes les étapes du projet;
- possibilité d'optimisation paramétrique du modèle résultant afin de minimiser les coûts de toutes sortes;
- travaillez avec divers indicateurs de l'algorithme, ce qui se reflétera dans l'amélioration des processus réels.
Formation de la cartographie des flux de valeur basée sur des graphiques standard etsymboles - blocs rectangulaires et triangulaires, flèches directionnelles et étagées et autres figures. Il permet d'enregistrer les étapes du processus à l'étude dans une seule langue pour tous les spécialistes. Dans le même temps, il est recommandé de différencier les symboles en fonction du flux considéré - matériel ou informationnel.
Lean Value Stream Mapping vous permet d'identifier tous les endroits où les éléments inutiles s'accumulent.
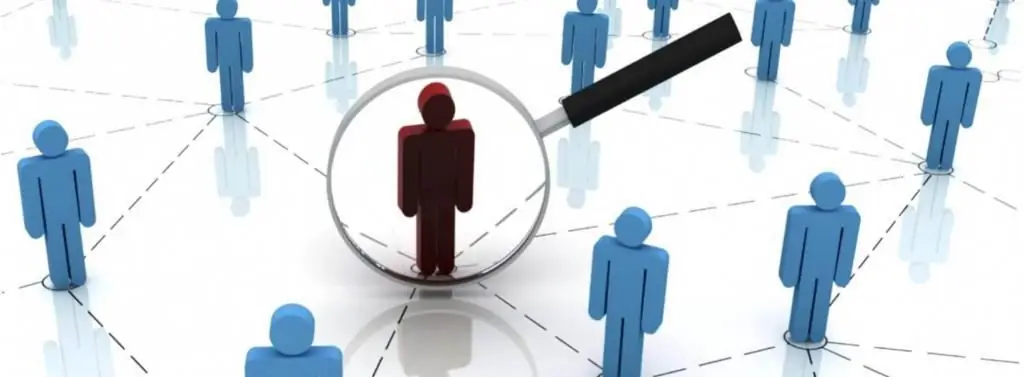
Règles de construction
Le mappage de flux de valeur implique une série d'étapes simples qui créeront rapidement le modèle de projet requis avec des paramètres donnés. Par exemple:
- Effectuer une analyse des flux de matières et d'informations afin d'obtenir une image fiable de l'état actuel du processus.
- Parcourez les flux dans le sens aller et retour afin d'identifier les causes cachées des pertes et de trouver des schémas négatifs.
- En aucun cas, prenez vous-même des mesures de temps, sans vous fier aux résultats d'autres spécialistes ou à des valeurs standard.
- Si possible, créez également une carte par vous-même, ce qui permettra d'éviter à la fois les erreurs des autres et les solutions de modèle.
- Concentrez-vous sur le produit lui-même, pas sur les actions des opérateurs ou des équipements.
- Construire une carte à la main, en utilisant un crayon ou des marqueurs.
- Visualisez les éléments d'un processus en utilisant des couleurs pour améliorer la perception.
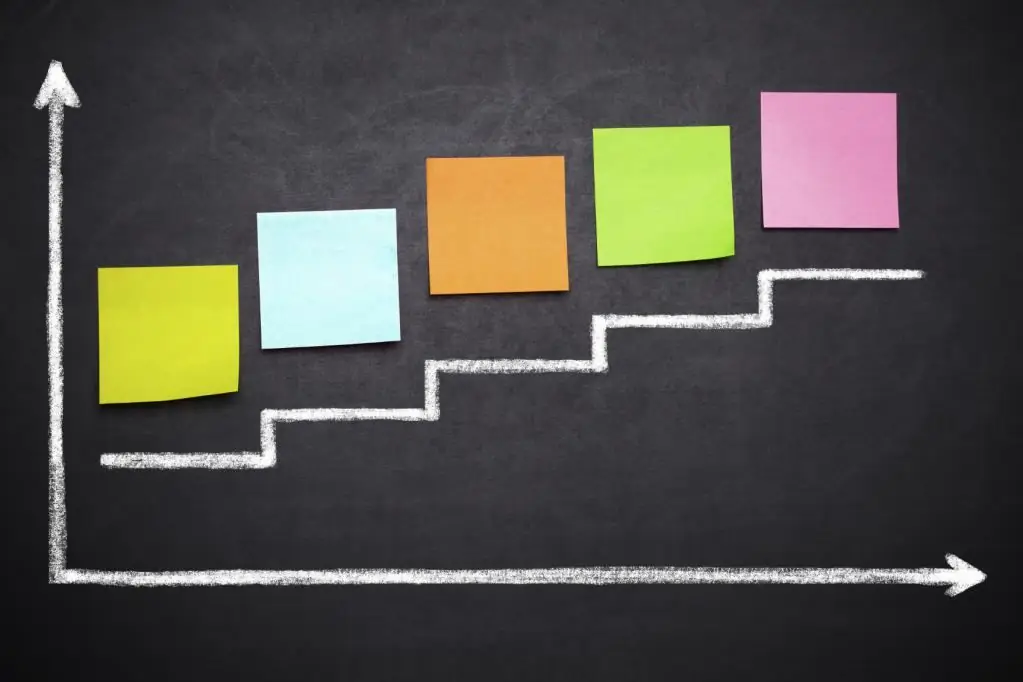
Exemples de mappage de flux de valeur
Prenons un exemple de création d'une carte de flux dans le domaine de la gestion de documents, inhérente aux activités de toute institution.
La tâche principale est de choisir le meilleur fournisseur. Le processus de décision standard est le suivant: sélection d'un fournisseur (12 jours) - exécution du texte du contrat (3 jours) - coordination dans les services fonctionnels (18 jours) - visa d'une personne habilitée (3 jours) - obtention du sceau du chef (1 jour) - obtention de la signature de la contrepartie (7 jours) - enregistrement auprès des autorités (3 jours).
Total nous obtenons le temps requis pour obtenir le contrat requis - 48 jours. Le résultat de l'analyse a été la découverte des goulots d'étranglement du schéma décisionnel.
Principaux changements après analyse de la carte:
- Une ordonnance a été prise pour déléguer la signature d'une partie des documents aux chefs de service (allègement de la charge de l'appareil administratif et réduction significative du nombre d'approbations).
- Les mêmes exigences ont été développées pour tous les services (une compréhension commune des exigences des documents contractuels, une diminution du nombre d'erreurs par les exécutants).
- Le principe d'analyse documentaire de bout en bout a été mis en œuvre en créant un groupe commun de spécialistes de différents services.
- Utilisation de nouveaux modèles de contrat.
- Les mécanismes de traitement de la documentation via le système électronique ont été optimisés.
- Un système électronique de suivi de la qualité des documents passant par les étapes du processus a été développé.
Résultat principalla cartographie de la chaîne de valeur est devenue une réduction par 2 du temps d'obtention de la documentation contractuelle, y compris le temps d'approbation dans les services départementaux.
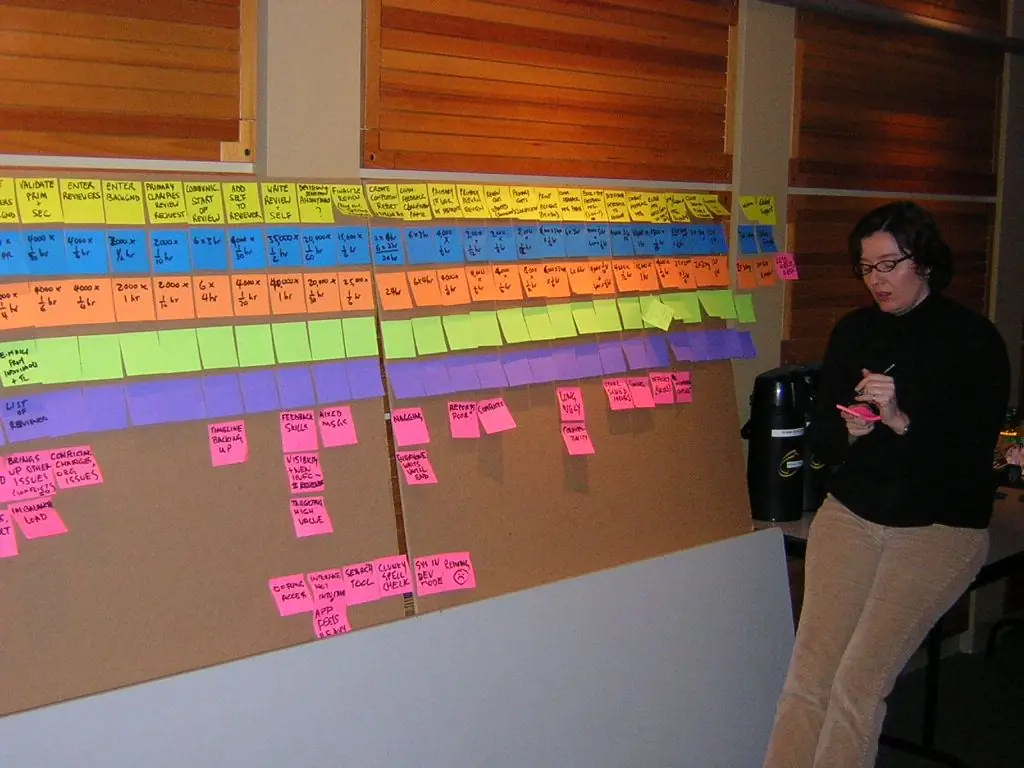
Conclusion
Récemment, la cartographie des flux de valeur (VSM, Value Stream Mapping) est devenue une méthode très courante pour optimiser le travail de diverses organisations. Cela est dû à sa simplicité et à son accessibilité, à des coûts minimes avec un effet bénéfique qui s'accumule au fil du temps. Il existe de nombreux exemples de mise en œuvre réussie de cette méthodologie logistique de production de base: entreprises de la Rostec Corporation, Transmashholding, chemins de fer russes, etc. Récemment, un système de fabrication allégée a été créé au niveau fédéral dans les établissements médicaux. En particulier, il est proposé de réaliser une cartographie des flux de valeur dans les polycliniques.
Comme vous pouvez le voir, le plein potentiel de la méthode considérée commence à peine à être révélé.